Monday 28 October 14.00 - 18.00 Part 1 Language: English
Tuesday 29 October 2019 14.30 - 17.30 Part 2 Language: English
Energy, Oil & Gas Session
SPONSORED BY 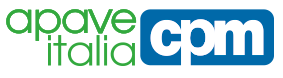
Monday 28 October - Part 1
14.00
Emiliano Costa, RINA Consulting
Mikel Garcia de Albeniz, Bionic surface technologies
Edoardo Ferrante, RINA Consultin
Stefano Barberis, RINA Consulting
Peter Adrian Leitl, Bionic surface technologies
Giuseppe Piscitelli, Rina Consulting
Andreas Flanschger, Bionic surface technologies
Use of Micro Structures to Increase Turbomachine Performance
The enhancement of the turbomachinery efficiency is becoming more relevant in order to increase their environmental sustainability and reliability. Thanks to the effect of micro structures applied over certain surfaces viscous losses can be reduced. These structures, called riblets, consist of tiny streamwise grooved surfaces which reduce the drag in the turbulent boundary layer. They could reduce the frictional resistance of flat surfaces up to 10%. This effect is significantly higher for 3D bodies since it also positively affect flow separation. In the frame of Resistant Project, their effect on a centrifugal gas compressor was studied via CFD (Computational Fluid Dynamics). The effect of the presence of riblets on the diffusor and volute was analysed. Those are the areas with higher losses, and thus, where the potential of the riblets can be exploited at best. The final goal of the project is to give a precise evaluation about the benefits in terms of efficiency increase and an estimation of the optimal riblets’ geometry.
14.20
Attilio Brighenti, S.A.T.E. Systems and Advanced Technologies Engineering
Davide Duranti, S.A.T.E. Systems and Advanced Technologies Engineering
Debora Quintabà, S.A.T.E. Systems and Advanced Technologies Engineering
Real-time simulation of gas turbine systems
Dynamic simulation of turbomachinery by Hardware in the Loop (HIL) real time systems has become an essential practice, due to the high cost of real equipment testing and the need to verify the control and diagnostic systems’ reaction to emergency situations. The authors developed a full model of a power generation Gas Turbine Plant, including liquid and gaseous auxiliaries, and the electrical generator and starter motor, integrated in a MATLAB®/Simulink® simulation suite, referred to as TGSim Plus™, which allows simulating steady state and transient conditions, such as complete start-up & shutdown operations as well as emergency, contingent operations and artificially injected fault scenarios. The model solver runs real time steps at milliseconds scale. The paper describes the main modelling characteristics and typical results of steady state and transient simulations of a heavy-duty gas turbine under development.
14.40
Alberto Clarich, ESTECO
Luca Battaglia, ESTECO
Design Optimization, cost and risk analysis of CNG vessels transportation
The GASVESSEL Project, financed by the EU under H2020, aims to prove the techno-economic feasibility of a new CNG (Compressed Natural Gas) transport concept, enabled by a novel patented Pressure Vessel manufacturing technology and a new conceptual ship design including safe on- and off-loading solution.
In this paper we illustrate how the software from ESTECO, modeFRONTIER for the process automation and optimization and VOLTA for the web-based collaboration and decision making, have been used by the partners in the different phases of the Project for the design of the system.
In function of each different geographical scenarios (which includes East Mediterranean, Barents Sea and Black Sea) and gas demand, parameters such as ship size and number, storage and facilities units at the ports have been optimized in order to reduce the transportation costs and therefore gas tariff.
Components of the gas vessels, in particular material and type of the fibers that wraps the liner, have been then optimized to minimize weights while respecting high value of safety factors.
Finally, an ongoing CFD study is performed to analyze the risks related to gas leakages and explosions.
15.00
Diego Barcella, OMB Valves
Thermodynamic analysis of sealing weld
In the valve industry for oil & gas applications, the tightness of many components is ensured by coupling with interference; for high temperature applications, if the coupled components have different thermal expansion coefficient, the dilatation due to the thermal cycles could bring to excessive plasticization phenomena, hysteresis, loss of interference and consequent leakage of the valve.
For these cases, a FEM analysis is a useful tool to predict the real capacity of the valve to guarantee the seal in the most varied working conditions, and in case of problems to prepare solutions.
One of the possible solutions is usually to weld the components together: in this case, however, it is still necessary to perform a thermodynamic and non linear elastoplastic calculations with finite elements. The simulation of weld process is fundamental to ensure that the heat input and the consequent localized thermal distortion does not overload the valve excessively, does not strain the sealing components unexpectedly, and that the residual stress added to those due to the operating conditions guarantee the pressure vessel resistance according to the international standards.
15.20
Andreas Spille-Kohoff, CFX Berlin Software
Jan Hesse, CFX Berlin Software
Rainer Andres, CFX Berlin Software
CFD Simulation of a Two-Sided Screw Compressor with FEM Simulation of Pressure Load
Two-sided (or double flow) screw compressors have the advantage of balanced axial forces, i.e. no axial forces act on the bearings, and that both bearings are at atmospheric pressure. Since the rotors are longer, they are more sensitive to bending due to pressure loads. We show results for the CFD simulation of a 4-6 screw compressor with SRM profiles, built-in volume ratio of 3, and rotor lengths of 336 mm at different rotation speeds and pressure ratios from over-compression to under-compression.
For high pressure loads, FEM simulations of the rotors were done to calculate bending lines. E.g. for 12,333 rpm and compression from 1 to 6 bar, male rotor is bent 5.1 µm outwards and 4.5 µm downwards, female rotor 7.2 µm outwards and 7.1 µm downwards (radial gap size between straight rotors and housing is 50 µm). New meshes around the rotors were generated with TwinMesh that take these bending lines into account, and CFD simulations for bended rotors are shown and compared to the cases with straight rotors. Due to increased gap sizes on pressure side and between the rotors, gap losses are higher and mass flow rates lower for the bent profiles. The average mass flow rate drops by 4%.
15.40 - 16.10
BREAK TIME
16.10
Marcus Reis, ESSS
CFD – DEM Coupling for Modeling of Fluid Flow with Accurate Particle Representation
Particle laden flows are encountered in many industries including oil and gas, agroindustry, pharmaceutics, mining, and many others. Eulerian granular and Langrangian approaches in multiphase CFD are commonly used to model fluid-particle flows for some these applications. However multiphase CFD has limitations due to the lack of constitutive models that adequately describe the range of particle characteristics. The coupling between DEM and CFD is a promising approach and broadens the range of particle-fluid processes that can be handled with numerical simulation. This presentation will provide an overview and latest development of modelling approaches for the simulation of both dilute and dense-phase fluid-particle flows. In addition, the coupling approach for Rocky DEM and ANSYS FLUENT will be showcased, with few interesting applications examples for modeling complex flows where fluid details are needed and key interest involves model particle shape, particle break-up, separation, segregation and mixing.
16.30
Koji Yamamoto, CYBERNET SYSTEMS CO
Prediction of mechanical chacteristics of electrode considering sand-like microstructure
Recently, improvement of energy density and durability for rechargeable battery become more and more significant due to motorization of automobile. It is important to evaluate electrode's mechanical characteristics which strongly affect overall battery performance. However, the analytical prediction is not easy due to sand-like complex microstructure made by active materials and electrolyte and so on.
We are trying to clear such problem by multiscale analysis approach based on homogenization technique using ANSYS and Multiscale.Sim. In this presentation, we will introduce some results of this trial which will be including
- CAD modeling for complex microstructure.
- Material behavior under virtual volumetric compression testing.
- Curve fitting the response of testing by Dracker Prager model.
16.50
Stéphane Velut, Modelon AB
Platform for Microgrid Design and Operation
This paper describes the design and operation of microgrids using Modelon’s Thermal Power Library and Modelon Impact, a web-based modelling and simulation platform.
For the purpose of this paper, we have designed and optimized two micro-grid systems. The first one is focusing on the design of battery for peak shaving and on the operation for demand charge reduction. The second one is a multi-energy system that is optimally operated by exploiting both thermal and electrical storage systems.
Modelon Impact has been developed as a flexible platform based on open-standards that can be used to efficiently solve current and future engineering problems for distributed energy sources and storage systems. Using a unified architecture, collaboration and efficient workflows are enabled.
17.10
Gabriele Milanese, University of Genova – DIME
Carlo Cravero, University of Genova – DIME
Advanced Axial flow Fans: an Integrated Design Platform for Industrial Applications
The current work covers the development and application of a design procedure for advanced axial flow fans, suitable for whatever industrial configuration. The attention is focused on the fluid-dynamic design of the fan blades geometry that, starting from a preliminary definition, is refined through different steps, progressively taking into account all the flow features. A single geometry modeler, coupled with different solvers of increasing complexity/fidelity, allows an efficient control of local flow characteristics (e.g. blade load in presence of strong sweep/lean effects) and the related global performance.
The entire process is suitable for different kinds of parametric analysis (e.g. DOE, Optimization, Uncertainty Quantification) and different levels of computing power (e.g. from notebooks to parallel architectures). Example applications have been carried out and main results are presented.
Tuesday 29 October - Part 2
14.30
Roberto Biondi, Ansaldo Energia
Michele Raciti, Ansaldo Energia
Fabio Parodi, Ansaldo Energia
Demetrio Scarfone, Ansaldo Energia
Michele Andreoli, EnginSoft
Giovanni Falcitelli, EnginSoft
Emiliano D'Alessandro, EnginSoft
Aero-Vibro-Acoustic analysis of high inertia flywheel for electric power system with low or zero inertia generators
To achieve the carbon dioxide emission reductions, many countries has increased their renewable generation capability. This process is leading to a particular impact on electric grid frequency control capability that is impeded if a minimum quantity of standard synchronous generators is not maintained connected to the electric power grid. One mitigation to counteract the issue outlined above which has seeing resurgence in popularity, is the installation of synchronous condensers coupled by high inertia flywheels which increases the global inertia of the electrical machine. The design of this flywheel has required to deal with several physics problem regarding to fluid dynamics, heat exchanging, Aero-Vibro-Acoustics analysis. In this paper, after a brief description of the flywheel 3D CFD model, a going deep on the Aero-Vibro-Acoustics analysis carried in Ansys with DAVA method will be presented, in order to show a calculation of the radiated acoustic power by the flywheel.
14.50
Andreas Spille-Kohoff, CFX Berlin Software
Jan Hesse, CFX Berlin Software
Rainer Andres, CFX Berlin Software
Co-simulation of 3D CFD model for positive displacement compressor and 1D CFD model of connected system
Rotary positive displacement (PD) compressors are used in industry as compressors to compress process gases, as vacuum or backing pumps to evacuate vessels, or as expanders to gain energy from pressurized gases. The 3D CFD simulation of such PD compressors is complex and time-consuming due to its transient nature and fine meshes; mesh generation has to properly represent radial and axial gaps in the range of some µm with PD machine dimensions up to metres to capture leakage flows, and heat transfer to rotors and the casing needs fine mesh resolution.
Due to this complexity, 3D CFD simulation should focus on the component, i.e. the compressor, and the attached overall system with vessels, valves, pipes, and consumers should be simulated in a 1D network or system simulation. Due to strong oscillations in the gas flow of PD compressors and their interaction with its system through pressure waves, a transient coupling is necessary.
We show results for a simple pressure pulse travelling through a pipe system as a verification case, a vane pump with pipes at inlet and outlet, and the starting behaviour of a screw compressor from atmospheric pressure to operating pressure 3 bar against a closed valve that opens at operating point. The compressor is solved with ANSYS CFX in 3D, the surrounding network of pipes, valves, losses and air chambers (as nodes) is simulated with Flownex in 1D, and boundary conditions are interchanged between Flownex and ANSYS CFX each time step: Mass flow rate and average temperature are transferred from ANSYS CFX to Flownex, static pressure and, in case of backflow, temperature in opposite direction.
15.10
Giuseppe Rocco, Flowserve
Giancarlo Cicatelli, Flowserve
Davide Balconi, Flowserve
Alessandro Montalbano, Flowserve
Numerical investigation of the leading edge shape effects on the NPSHi, design insight and experimental validation
Cavitation is a very complex phenomenon that affects turbine and pump impeller performance and life. This phenomenon is due to the evaporation of the liquid when it flows through a low pressure region. In the case of centrifugal pumps the effects of cavitation have a strong impact in terms of noise, Head loss, and blade damage. Classic 1D theory provides some insight to the pump engineer for the design of a new impeller but it’s totally inadequate to account for extreme design (very low NPSH 3%). Instead an accurate CFD analysis can provide excellent numerical results and useful insight for non-standard design. The present work deals with a numerical analysis of the flow inside a centrifugal pump with a focus on the leading edge design. In particular this analysis shows that an ad hoc rounded shape of the leading edge of the impeller provides smooth pressure distribution on the blades and therefore a mitigation of the cavitation effects. The experimental results confirms that the non-standard design provides an optimal improvement of the suction performance of the impeller.
15.30
Thomas Tripolini, Gamma Meccanica
Fabio Villa, EnginSoft
Parametric CFD simulation of a Melting Furnace For Stone Wool Production Lines
A CFD simulation of a Melting Furnace For stone Wool Production Lines is presented in the current paper. The simulation is performed using the software ANSYS FLUENT® R1-2019. Simulation of a Melting Furnace is a complex multiphysic simulation that involves different physical areas (fluid dynamic, heat transfer and electromagnetism). According with the customer Gamma Meccanica S.p.A., a parametric geometry of the furnace is realized, in order to study a possible improvement of the electrodes configuration, in term of dimension and position. The paper describes the selected models, that are included in ANSYS FLUENT® by default, to simulate the electrical fields in conjunction with the melting process of the stone wool (due to the joule effect). The outcome of these simulations are the characterization of temperature distribution inside the molten stone in function of the defined parameters and the evaluation of heat losses from the molten stone to the external environment. Suitable hypothesis are used in these work to achieve a reasonable computational time. The presented simulations are current used by the customer Gamma Meccanica S.p.A. to improve the design of the future furnace.
15.50 - 16.20
BREAK TIME
16.20
Mattia Ricci, NIER Ingegneria
Benedetta Baldisserri, NIER Ingegneria
Stefano La Rovere, NIER Ingegneria
Virtual prototyping for design by analysis of ITER systems
The ITER project has the scope to design, construct and operate an experimental nuclear fusion facility representing the first fusion device to produce net energy. The Electron Cyclotron Upper Launcher (EC UL) is a sub-system of ITER with the main functions to perform EC heating and current drive, to perform plasma control and to assist plasma start-up. The EC UL includes the structural part (Port Plug), the related in-vessel items (nuclear shielding, blanket module and optical components) and the flange (bolted to the Vacuum Vessel) providing the first confinement for tritium and dust.
The work that has been given in charge of NIER is necessary for the validation of the EC UL design since no physical prototype is foreseen to be performed: the complexity of the geometry and of the load conditions required to be taken into account, do not allow the execution of tests on prototype for the qualification of the design.
Two particular cases are going to be presented, which prove the efficacy of the NIER support. For both cases, NIER detected the issues and found the modifications on the design that allowed it to satisfy both the criteria of the construction code and the relevant functional limits.
16.40
Luis Rubio, ELTE University
László E. Kollár, ELTE University
Multi-phase Fluid Struture Interaction for 3D Wind Turbine Blades
Numerical methods approaches to study complex systems save time and money in nowadays industries. In this work, a comprehensive methodology for studying 3D wind turbine is presented in order to investigate the behaviour of the system. ANSYS software, FENSAP-ICE and FEA packages, is used for this purpose. FENSAP-ICE solves the equations of the multi-phase fluid, cold wind and super cooled droplets; mass and momentum conservation of the multi-phase flow in a pre-defined volume -domain. It is imported as a load, in FEA package, in order to calculate the mechanical behaviour of the blades. Blades are composed by orthotropic composite material, which is lately used in Eolic industry for this purpose. Moreover, the angular velocity of the blade is considered as centripetal load. FEA analysis results in the study of the deflection/deformation of the blade, equivalent stress (Von-Misses) and, force and moment reaction. Finally, theoretical results given by ANSYS are presented and analysed.
17.00
Eunsil Han, Taesung S&E
Jeongpil Hwang, Taesung S&E
Dynamic Analysis Method of Floating Solar Structures using AQWA
Recently, there is interested in renewable energy have gradually increased. Nowadays, Floating photovoltaic system is a new power system using the water surface above the dam, reservoir water, and ocean. This market is expected to be expanded because the floating photovoltaic system is different from the traditional approach to the development of a solar power system causing problems such as environmental degradation. This paper introduces the hydrodynamic analysis method of floating solar structures using ANSYS AQWA and the method of structural analysis of solar structures considering the response characteristics over time.