Monday 28 October 2019 14:00 - 17:30 Event - Language: English
The RecurDyn Experience
All current market research predicts that multi-body-simulation is the area of CAE where the highest growth rate is expected to occur in the coming years. While multi-body simulation will remain a topic for a relatively small community of specialists, this discipline will be crucial in many industrial contexts. For instance, advanced mechatronics applications require the development of accurate control systems and multi-body-simulation provides the most effective support for designing, developing and testing controls. In addition, multi-flexible-body simulation is a valid approach for accelerating the design of transmissions, machine tools, and packaging machines because it enables engineers to reproduce and understand what really happens to components while they are in motion. RecurDyn is software designed to undertake these types of investigations. It delivers the most up-to-date digital environment to copy real life at any level of detail desired.
Don't miss the opportunity to enroll for and contribute to this seminar: bring your curiosity, your doubts and your requirements. Industrial users, researchers, and software experts will be on hand to introduce you to the world of RecurDyn and multi-body-simulation.
AGENDA
14:00
Optimizing Equipment Design with RecurDyn - EDEM Co-Simulation
Carles Bosch Padros, DEM Solutions Ltd., UK
RecurDyn multi-body dynamics simulation is an essential tool in the design of industrial equipment providing engineers with insight into machine performance. It is key that accurate loads are used in such simulations to have reliable results. For many applications, those come from the ground or rocks. Due to the nature of those materials, prediction of such loads is challenging.
EDEM is the leading bulk materials simulation software, providing engineers with accurate material flows resulting in equipment loads. It is used in multiple sectors to optimize equipment and processes. The RecurDyn-EDEM co-simulation enables bulk material loads to be used in RecurDyn during simulation for increased realism in equipment motions and a deeper understanding of how bulk material loads are transferred throughout a mechanical system. The RecurDyn-EDEM solution reduces the need for prototyping, allowing designs to be evaluated for different process conditions early in the design cycle. This presentation provides an overview of RecurDyn-EDEM co-simulation with application examples. It also introduces a new flexible geometry capability that enables prediction of deformation of individual parts for greater insight into real-world systems.
14:30
Human Body Models for System Dynamics Simulation with RecurDyn
Valentin Keppler, Biomotion Solutions, Germany
Nowadays the importance of multibody simulation increases continuously. However, mechanical simulation results like forces or accelerations often are not the main focused quantities. Today’s challenge is to analyze and optimize (and understand) complex, connected systems. This means we have to provide sub models for all relevant involved sub-systems. Many, if not most systems / products are designed to interact with humans as e.g. occupant, driver, or operator. Therefore, it is obvious, that some of the products key performance indicators (KPI) are related to this biomechanical human-product interaction. This interaction can be passive (vibration exposure, injury risk assessment in collaborative robot environment) or even depending from the human motion (exoskeleton).
In the presentation, we will explain on some examples how human body models in RecurDyn can be used in conjunction with technical system models to analyze the system dynamics with respect to human-relevant KPI.
15:00
Evaluation of the Transient Dynamic Behavior of Machine Tools in a Multidisciplinary Environment
Timo Giese, FunctionBay GmbH, Germany
RecurDyn software offers plenty of options to simulate the dynamics of machine tools, going from single components up to system level. The FBG.MachineTool module packs multiple features to automate the modeling and the simulation of machine tools.
In this presentation, a typical machine tool is investigated through coupled domain simulation involving structural / thermal FEM and control systems.
15:30
Break
16:00
Automatic Machine Capacity Improvement through Motion Law Optimization and Multibody Analyses
Davide Marini, EnginSoft S.p.A., Italy
Capacity is the most important property of an automatic packaging machine, since it sets its competitive advantage. This project focused on a machine, designed and built by OPEM SpA, for the production of coffee capsules.
The challenging goal was to increase its capacity by 25%, without affecting the architecture and size of the machine. OPEM and EnginSoft achieved the target by optimizing the laws of motion of all actuators. As the dynamics became then more severe, all effects were investigated and validated by performing a number of multi-flexible-body simulations in RecurDyn software.
16:30
Design and Validation of Compression Springs for High Performance Engines
Thomas Kelichhaus, FunctionBay GmbH, Germany
Progressive compression springs are widely used in valve trains and/or fuel injection systems of higher performance engines. In previous times the spring layout and manufacturing was typically performed by the spring providers with a subsequent testing by the engine manufacturer. Later this development process could be improved by numerical spring validations based on Multibody – Dynamics (MBD) simulations.
Starting from the requested spring data sheet, which is mainly calculated by the spring provider by applying theoretical compression spring formulas, the spring manufacturer then tries to wind the spring on their coil winding machines in a way that it matches decisive spring design criteria like the F1/L1, F2/L2 force – displacement relationships within a given tolerance. On the other hand, the analyst tries to create an MBD simulation model based the same original data sheets. In many cases simulation results and measurements cannot be aligned well because the winding curve of the produced spring differs from the theoretical one derived for the MBD simulation. In addition, the spring provider, who is typically responsible for the spring layout, often has only limited access to the exact valve train or fuel injection design, which sometimes leads to an extended number of design cycles.
This paper describes a new approach to develop and validate a compression spring design based on a combined MBD and non-linear flexible body simulation environment. Since the basic spring layout can also be found within this toolkit, it significantly shortens the overall number of design cycles. The outcome is a validated spring layout including an optimized winding curve, which then can be forwarded to the spring provider for an appropriate manufacturing.
17:00
Increasing the Reliability of Multi-Body-Dynamics Simulation by coupling Parameterized RecurDyn Models with modeFRONTIER Multi-Objective Optimizer
Fabiano Maggio, RecurDyn Europe GmbH, Germany
The value of any multi-body model is strictly dependent on its reliability. When a model does not return the same values we measure on a physical prototype, then it is about useless. Unexperienced users tend to associate the reliability with correctness, but it is not enough: even the rightest models can return unrealistic outputs. This mainly happens with non-linear models, which greatly amplify the effects of non-correct inputs.
In absence of better information, the user assign nominal values to inertia, stiffness and damping coefficients. While this does not configure a mistake, it must be understood that real parts rarely have nominal properties and, consequently, the model outputs cannot match the real outputs. This triggers the need of tuning the input properties until the outputs become similar to the measured ones.
This presentation will introduce the topic explained above, referring to a real application case. Since the simultaneous tuning of multiple input properties to match multiple output measurements is definitely a multi-dimensional task, it cannot be performed manually. The most effective / efficient approach consists in coupling the parameterized model with optimization algorithms.
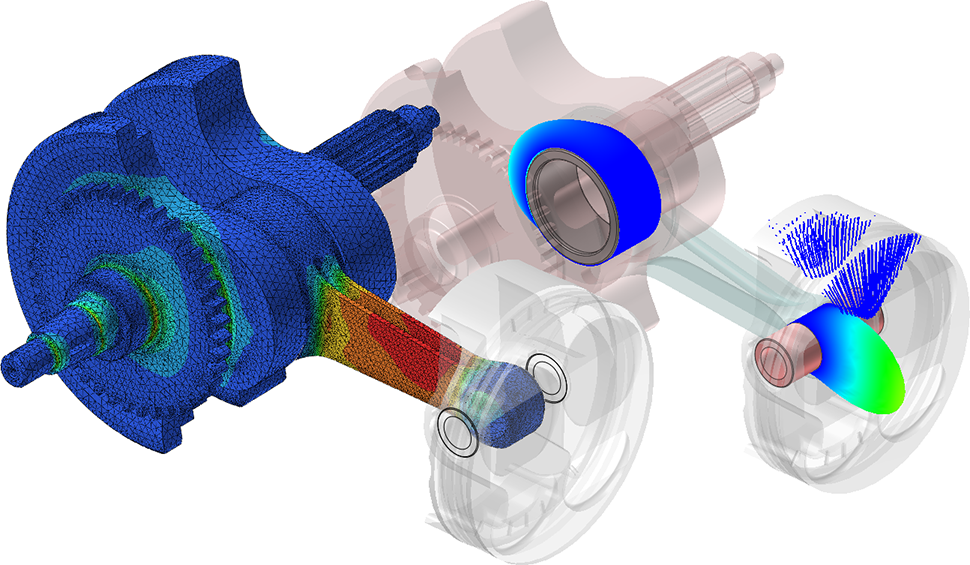
This event is organized by
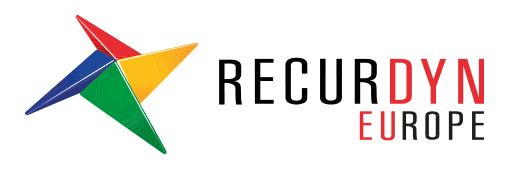